Welding Assessment Demystified: Trick Processes, Tools, and the Necessary Duty They Play in Maintaining High-Quality Welds
Welding assessment works as a critical backbone in the guarantee of structural stability and quality in welded joints, impacting various sectors from building and construction to production. This process is not just a rule; it encompasses vital strategies such as aesthetic evaluations and progressed non-destructive screening methods created to uncover problems that can compromise safety and security. With an array of specialized tools at their disposal, inspectors play a necessary duty in keeping high criteria. The complexities of these approaches and their ramifications for high quality assurance continue to be commonly ignored. What are the crucial processes and tools that make sure these criteria are supported?
Value of Welding Inspection
Making certain the honesty of welded joints is vital in various industries, making the importance of welding examination indisputable. The quality of welds directly influences the security, efficiency, and durability of structures and elements. In industries such as construction, auto, aerospace, and production, any type of failing in bonded joints can bring about devastating repercussions, consisting of architectural failings, tools breakdown, and death.
Welding examination functions as an essential quality assurance step, guaranteeing that welds fulfill specified requirements and regulatory needs. It identifies problems such as fractures, porosity, and incomplete combination that might jeopardize the stamina of the weld. By spotting these problems early, welding examination can prevent costly rework, delays, and prospective safety dangers.
In addition, welding inspection fosters compliance with market requirements and certifications, improving the trustworthiness of companies and their products. It additionally supports continuous enhancement by providing beneficial comments to welding personnel, enabling them to fine-tune their procedures and techniques.
Ultimately, the relevance of welding evaluation can not be overstated; it is vital for keeping high-quality welds, making certain safety, and protecting investments across numerous industries.
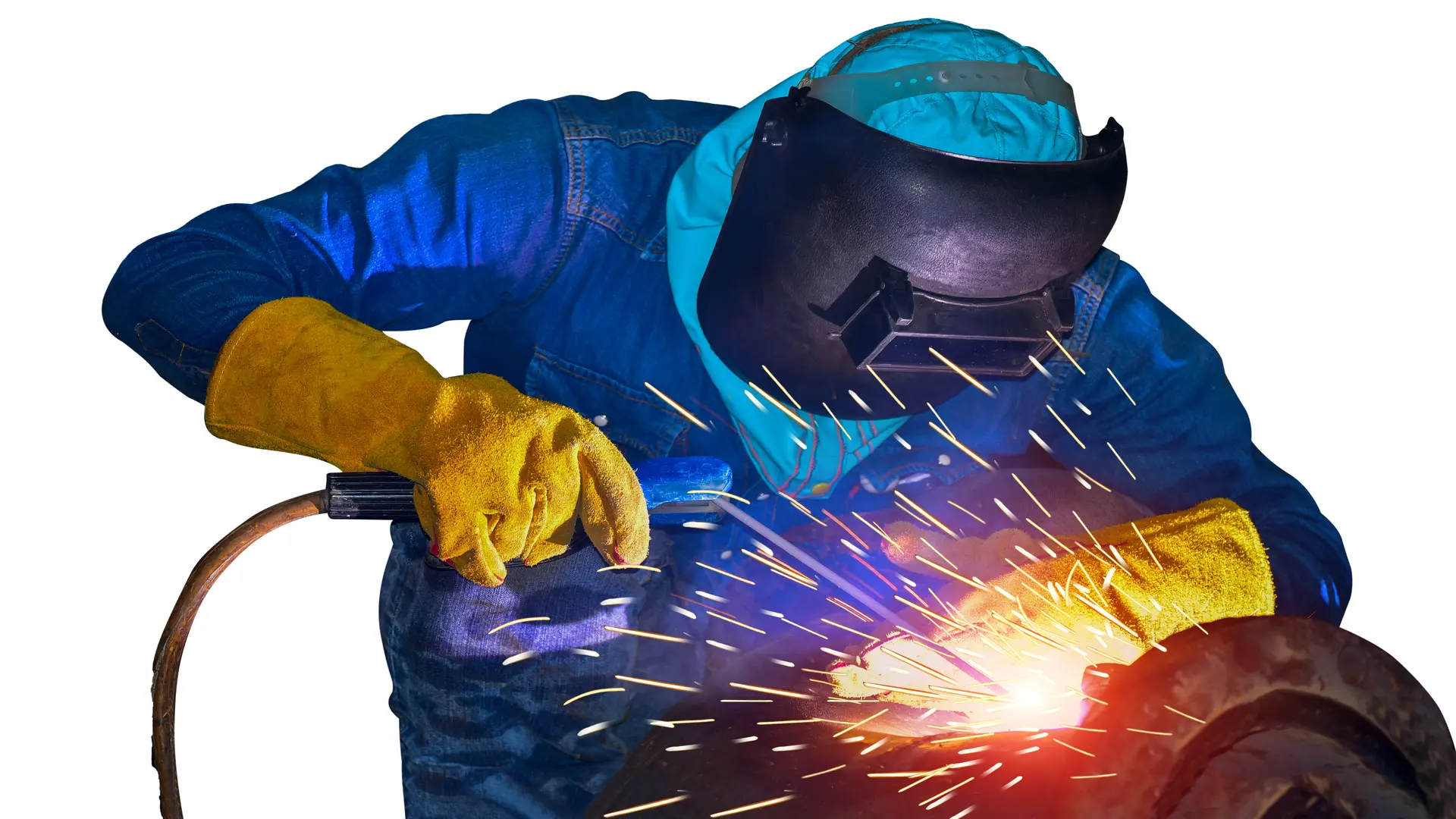
Key Assessment Processes
Effective welding inspection counts on a series of crucial processes created to review the top quality and stability of welds. These procedures encompass both non-destructive and aesthetic screening (NDT) techniques, making sure that any type of flaws are determined before they endanger architectural integrity.
The very first step in the inspection procedure is a complete aesthetic assessment, which enables inspectors to evaluate welds for surface issues such as splits, undercuts, and incomplete fusion. Following aesthetic checks, various NDT techniques might be utilized, consisting of ultrasonic testing, magnetic fragment screening, and radiographic screening. Each approach uses special benefits; for circumstances, ultrasonic testing can spot inner problems, while radiographic screening supplies a permanent document of the weld's internal structure.
In addition, it is vital to verify conformity with relevant codes and criteria, guaranteeing that the weld meets industry specifications. This includes checking weld dimensions and positioning, as improper dimensions can result in failures under lots.
Essential Tools for Inspection
Consistently utilizing the right devices is important for accomplishing accurate welding inspections. A thorough set of assessment tools aids make sure that welds satisfy stringent quality requirements and specs.
One of the main devices is the aesthetic evaluation gauge, which allows examiners to evaluate surface conditions, such as cleanliness and surface finish, straight. Additionally, calipers and micrometers are necessary for gauging weld measurements and ensuring they comply with needed tolerances.
For more detailed assessments, ultrasonic testing (UT) equipment is vital. This approach uses high-frequency acoustic waves to spot interior imperfections and evaluate material density. Magnetic particle testing (MT) and color penetrant screening (PT) are important for determining surface and near-surface flaws, supplying prompt visual indicators of possible issues.
Welders must also be furnished with solidity testers, which examine the mechanical residential properties of the weld steel and base materials, guaranteeing they satisfy specified needs. Ultimately, recording searchings for with digital examination devices enhances traceability and quality assurance. By utilizing these crucial devices, examiners can preserve premium welds, inevitably adding to the security and dependability of bonded structures.
Typical Problems and Their Discovery
Welds, akin to the backbone of architectural integrity in building and production, can exhibit different defects that jeopardize their performance and safety and security. Typical defects consist of porosity, cracks, undercut, absence of blend, and slag additions (Welding Inspection Gilbert Arizona). Each of these defects can manifest as a result of improper welding techniques, bad product choice, or poor prep work

Detection of these problems can be attained through different non-destructive testing approaches, consisting of aesthetic inspection, ultrasonic testing, and radiographic screening. Each method plays a critical duty in recognizing these mistakes, making certain that the honesty of the weld is maintained and minimizing the risk of failing in critical applications.
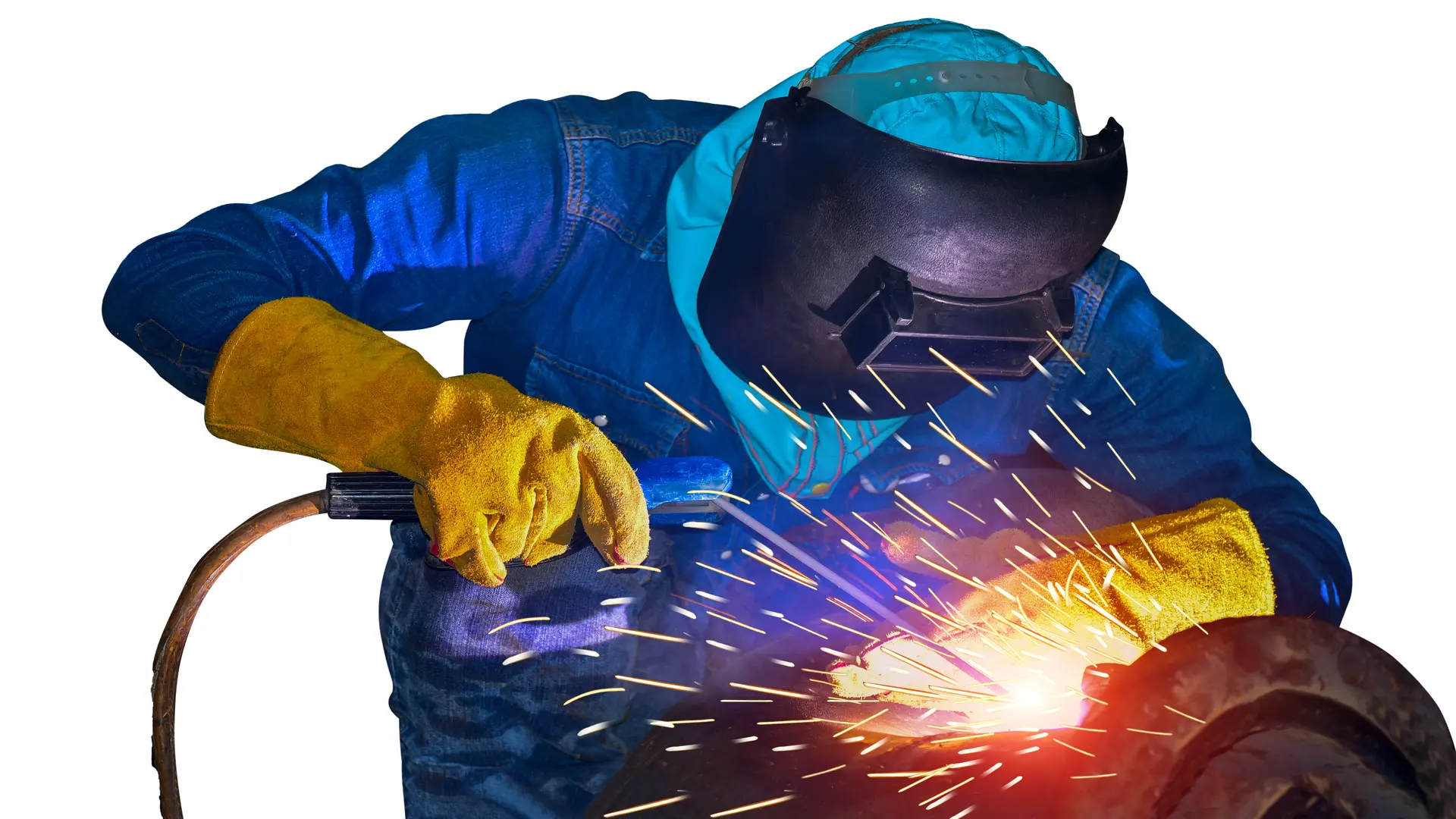
Finest Practices for Quality Control
Guaranteeing the finest quality of welds is vital for structural integrity and security, especially in industries where the repercussions of failure can be extreme. To achieve this, several best methods for high quality guarantee need to be executed throughout the welding procedure.
First, a robust welding procedure requirements (WPS) ought to be established, outlining the essential parameters for every welding procedure. This makes certain uniformity and adherence to sector requirements. Second, thorough training and qualification of welders are necessary; knowledgeable workers are better outfitted to create top quality welds and identify possible problems.
Regular examinations need to be incorporated right into the you can look here welding process, utilizing both aesthetic and non-destructive screening (NDT) methods to identify flaws at an early stage. Routine calibration of examination devices is essential to preserve precision. In addition, documenting all welding activities, consisting of evaluations and restorative actions, creates a traceable document that can be vital for quality assurance.
Verdict
To conclude, welding examination functions as a critical system for making sure the stability and integrity of bonded joints across markets - Welding Inspection Gilbert Arizona. Through the application of vital inspection procedures and the use of necessary devices, companies can effectively recognize and address prospective issues. Clicking Here Adherence to ideal techniques in quality control not just enhances safety however additionally guarantees conformity with sector criteria, inevitably adding to the durability and performance of elements and frameworks
Welding inspection offers as a crucial backbone in the assurance of architectural stability and quality in welded joints, influencing various sectors from building to production.Making sure the stability of welded joints is paramount in various sectors, making the relevance of welding examination indisputable.Welding evaluation serves as a vital high quality control procedure, ensuring that welds satisfy specified requirements and governing requirements. By employing these important tools, inspectors can maintain high-grade welds, inevitably adding to the safety and security and integrity of bonded structures.
In verdict, welding evaluation offers as a vital device for making sure the integrity More about the author and integrity of bonded joints across industries.
Comments on “Why Select Expert Welding Inspection Gilbert Arizona for Your Jobs?”